Test and Tag intervals vary from industry to industry, workplace to workplace and depend on what equipment is being used and where.
That’s already enough to confuse most people. The trouble is, there is a lot on the line. You need to know you have the very best when it comes to electrical testing and tagging services.
Workplace safety is a serious issue that too often goes unnoticed, is ignored or is not properly addressed.
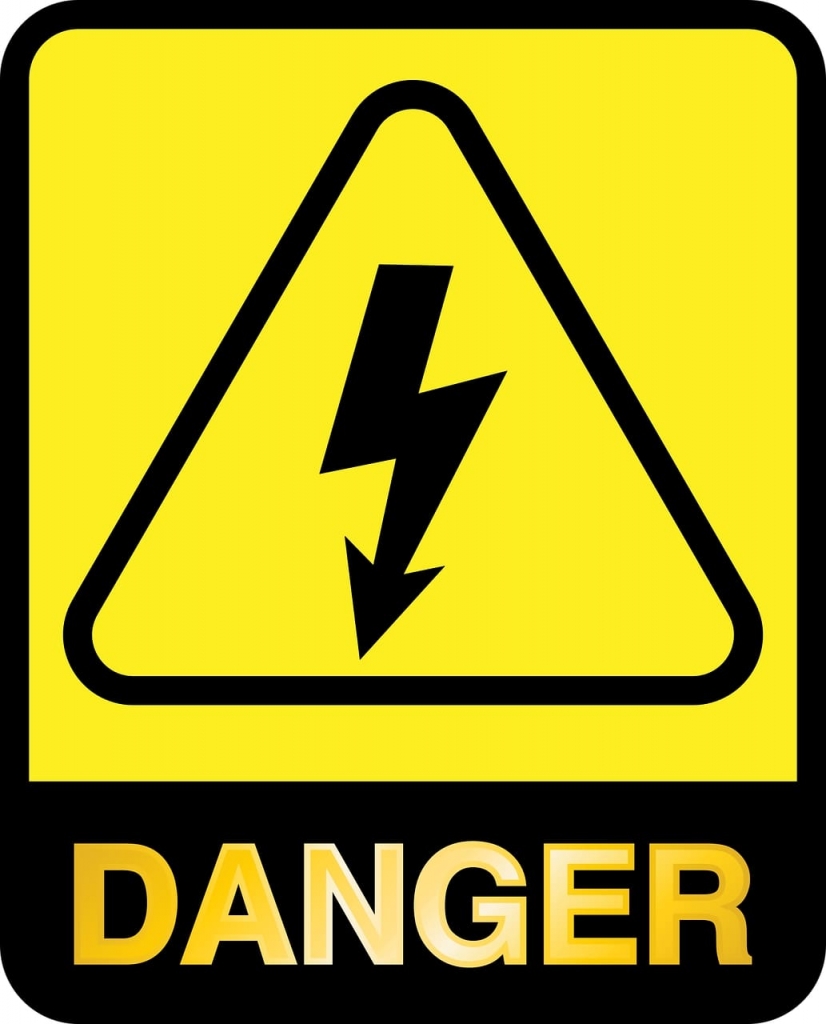
WorkSafe, the government’s own regulator admitted it had under-reported workplace deaths for some time. After aggregating data collected by police and other government agencies, WorkSafe announced in the six years from 2013 to 2018 there had been 413 deaths. That was up 40 percent from the 291 deaths previously reported.
Early in Dec 2020, a woman reportedly died after being electrocuted in a South Island workplace leading to a coroner’s inquest.
Whilst testing and tagging equipment and appliances doesn’t mean your workplace is safe from electrical accidents, it does significantly narrow the chances of a tragic event occurring.
Do you know what needs to be tested and tagged?
There are specific testing and tagging requirements that apply to each and every workplace across New Zealand.
Before you ask – How often do I test and tag? It is best to know what exactly needs to be tested and tagged.
All equipment that plugs into the power supply including tools, leads and RCDs must be regularly tested and tagged according the industry standards.
Different industries have different workplace standards that apply. The variables to each site cover key points such as when and where equipment is used and stored.
The AS/NZS 3760 standard is best taken as a minimum requirement.
Test and Tag intervals
Test and Tag intervals vary according to the workplace and the use of equipment.
As an example, it is outlined by Worksafe that “electrical equipment used on a construction site – outside and in damp conditions – would need more frequent testing than a computer in an office.”
The ongoing testing and tagging of electrical equipment and devices is vitally important and the frequency of test and tag intervals depends again on the industry.
This table gives you a good starting point.
- 3 Month Test and Tag intervals apply to; building, construction and demolition sites.
- These sites need the most frequent testing as there are considered a harsh environment. An appliance and any equipment are more likely to be damaged compared with other workplaces.
- 6 Months cover factories, warehouses, and production locations. Although these are not considered harsh environments, the use of appliances is constant and therefore needs to undergo test and tag intervals of 6 months.
- 12 Months testing and tagging apply to an environment where the equipment or power supply cord is prone to flexing, overuse, or open to damage. These sites are commonly referred to as hostile environments. The appliances or equipment can be exposed to dust, weather, and general deterioration.
It helps give you an answer of how often do I test and tag my equipment and appliances, but there still can be some confusion.
The added confusion of when to Test and Tag
With all the different scenarios of what test and tag intervals apply, it makes sense to give an example of how easy it is to be confused and have a dangerous workplace without knowing it.
If you look at the case of a simple extension cord, it shows how complex the issue can be.
If that extension cord is being used on a building site, it would need to be tested and tagged every 3 months. That very same cord would need to be tested and tagged in 6 months if it was used in a workshop environment. If it was being used in a work kitchen, then a yearly test would apply. If the extension lead was then used for connection by the I.T department in a Server Room then an even longer retest is required – up to every 5 years.
This illustrates how easy it is to have items ignored or forgotten when it comes to the correct test and tag intervals.
The added safety of a trusted professional Test and Tag team
Testing and tagging should always be carried out by a trained professional. You need someone who knows;
1. Which Worksafe standards apply
2. Which testing tools to use
3. How to correctly record any testing and tagging
4. The scheduling of each of the test and tag intervals
Having the complete details of the equipment or appliance test properly recorded and dated is one step. Knowing when the next scheduled test and tag is due means staying compliant.
There are strict legal obligations that cover a range of industries throughout New Zealand. That’s where a professional test and tag team can make all the difference.
With Jim’s Test & Tag NZ on your side, you have the top testing and tagging professionals looking after you and your workplace.
Having that expertise and experience to call on gives you complete peace of mind.
Jim’s Test & Tag NZ are still the only name you need to know for the best in skilled testing and tagging of electrical equipment, appliances and tools.
Have the experts visit your workplace and make sure your site is properly tested and tagged.
For more details, see our electrical testing and tagging services page. Jim’s Test & Tag NZ are here for you. For a free quote, contact us today.