Wherever there are appliances, there is a risk, which is why testing and tagging electrical appliances at the workplace is critical.
As an employer, it’s your legal responsibility to provide your employees with a safe, hazard-free workplace so far as is reasonably practicable. This includes the electrical devices and equipment. It can range from something as simple as using a toaster in the lunchroom, to using portable electric equipment like a grinder on a construction site, and more.
If it plugs into a power socket, it needs to be tested and tagged regularly.
Some risks associated with electricity
There’s a link between the risk of death or injury from electricity, to where and how it’s used.
The risks are higher when using portable equipment in damp surroundings or outdoors.
If you’re working in a cramped space with earthed metalwork, it might be difficult to avoid receiving an electrical shock if the equipment or appliance develops an electrical fault.
Some appliances and equipment can involve greater risk than others. Portable equipment including the plugs, sockets, electrical connections and the cable itself are vulnerable to damage.
Extension leads that are connected to equipment which is often being moved, can be more vulnerable to damage.
High risk workplaces can also contribute towards damage of appliances and equipment.
This includes:
- wet or dusty areas
- workplaces that use corrosive substances
- manufacturing environments
- commercial kitchens
Depending on the workplace, you may have additional duties to manage electrical risks. It’s important to know the classification of your workplace and the duties required.
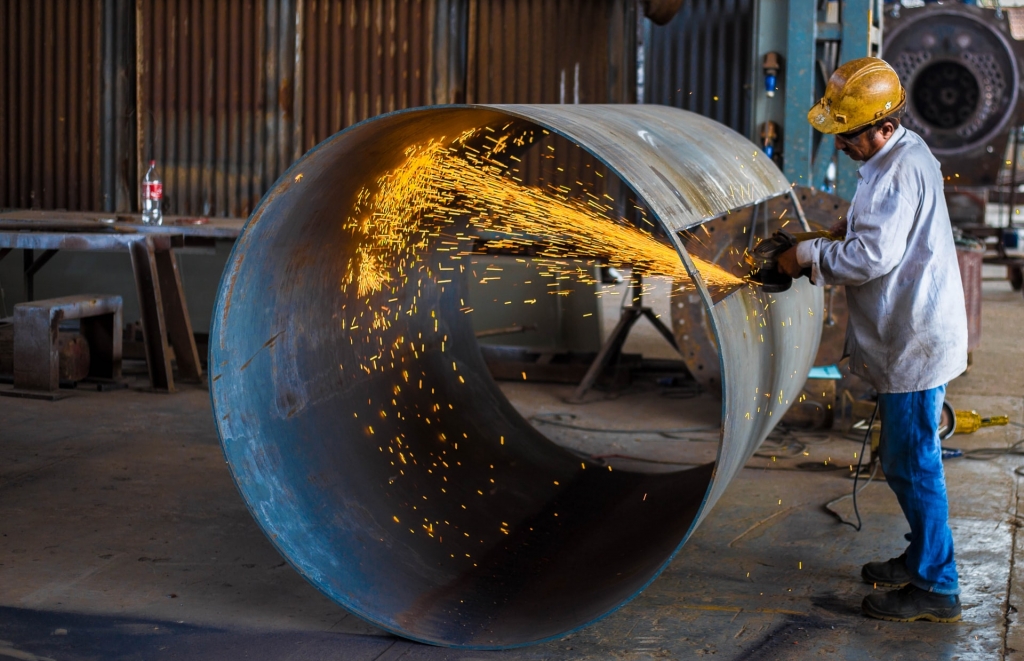
What problems can happen with electrical devices?
The older an electrical device gets, the more that can go wrong with it. Faults can occur at any stage of the life of an appliance, which is why even new appliances need testing. Knowing you have processes in place gives you peace of mind that the appliances are safe to use at the time of testing.
Some of the problems that can occur include:
- Frayed wires, cords, extension leads
- Damaged equipment caused by misuse, moisture, or exposure to harsh elements/chemicals
- Faults in the wiring
- Safety switches that don’t trip
- Current leakage
- Earthing system faults
- Lower insulation resistance
- And more
Problems such as there can jeopardize the safety of employees and visitors alike. It can result in anything from burns and shocks to electrocution and electrical fire. This is why appliance testing at the workplace is so important.
Testing equipments at the workplace can helps prevent any serious problems from occurring
These professionals are highly trained to identify any problems, especially those which are unseen, such as current leakage.
With thorough inspection and testing of appliances, any problems can be identified before an injury occurs.
As part of the process, the technician places test tags on any equipment that has never been tested and updates the tags on any existing appliances. Each tag has the name of the person who tested the equipment, the date of the test, and the date for when it needs to be tested again.
The technician also provides a report including any problems that are evident. It’s then your duty to act immediately to fix the problem and restore a safe workplace. It’s important to note, higher-risk workplaces using certain electrical equipment must use RCDs as an added safety measure.

Legal requirements as an employer
As an employer in New Zealand, you’re legally required to ensure all electrical equipment is safe to use and maintained in a safe condition.
In the event of injury or worse, you need to show you provided employees with all necessary steps to provide a safe workplace as far as reasonably practicable, otherwise the consequences for you and the business can be dire.
If you can’t show these steps, the end result can be anywhere from hefty fines to imprisonment for breaching safety regs. If you’re not sure whether your workplace is safe for staff, or if it falls under the category of a higher-risk workplace, you need to engage the services of a professional team without delay.
Jim’s Test & Tag team are the experts you can rely on
Jim’s Test & Tag are highly trained professionals in workplace inspection and testing. They specialize in identifying faults that are visual and non-visual and diagnosing those faults.
Jim’s Test & Tag uses certified equipment to do the electrical testing and tagging, is precise and thorough, and keeps accurate records.
Your entire workplace can be inspected and tested, along with all appliances and equipment. With accurate records, you’re protected on many levels, and you’ll know when the next appliance or equipment testing is due.
You can rely on Jim’s Test & Tag New Zealand.
Contact us or fill in the online form for a Free quote.