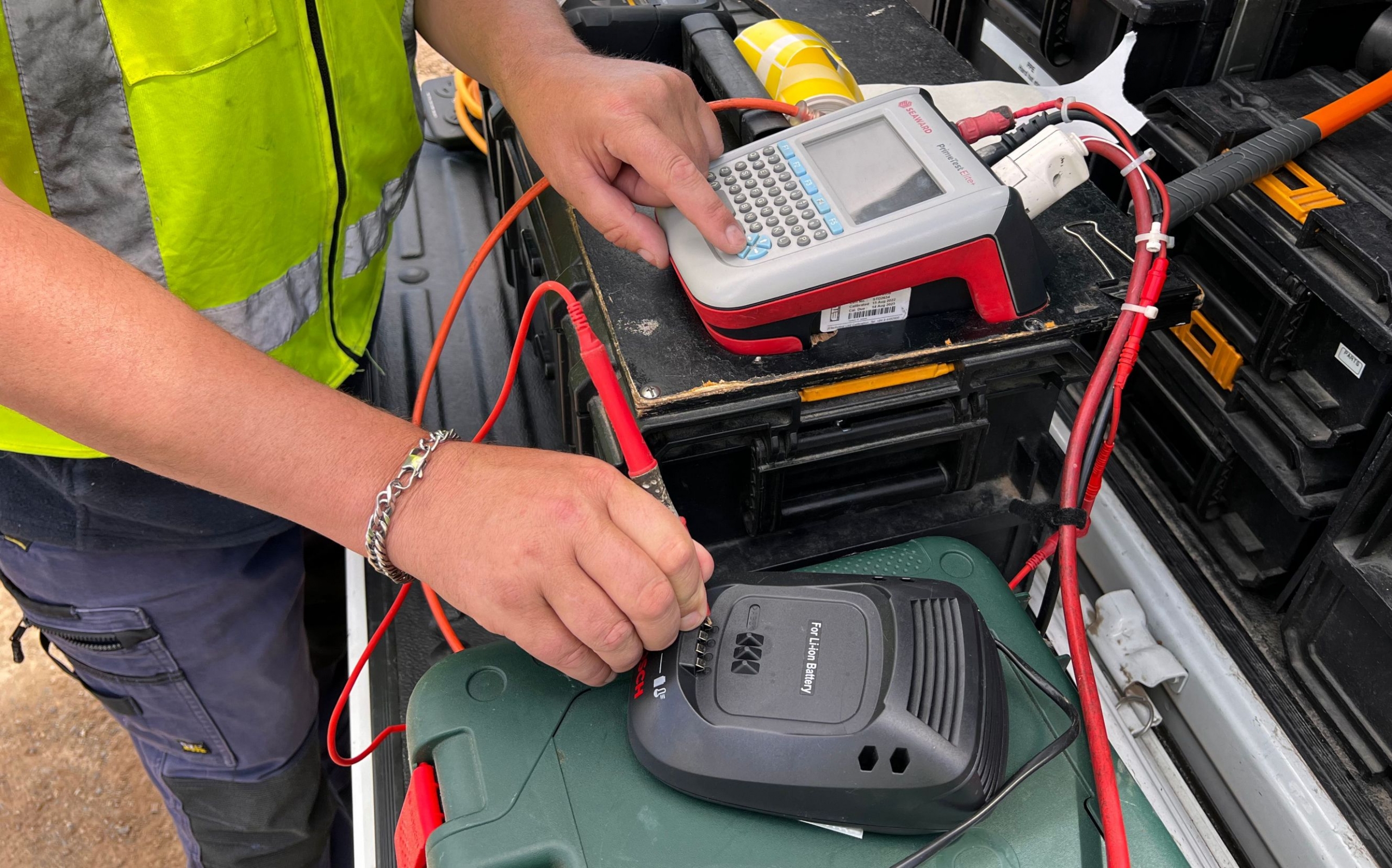
What is portable appliance testing?
Portable appliance testing is the process by which portable appliances are inspected and tested for safe use. These tests are conducted according to the AS/NZS 3760 or the AS/NZS 3012 for workplaces where electrical installations are in progress, as well as construction and demolition sites. The testing is completed with the use of a portable appliance tester device that helps to assess the safety status of each item.
Why is it important to test portable equipment?
While some safety defects are identifiable by visual examination, others can only be found by thorough electrical testing of equipment. By ensuring your tools, appliances, and equipment are safe, you are eliminating unnecessary risk. Every year, people are injured or killed at work. You can ensure that your workplace is safe by asking a Jim’s Test & Tag technician to test and tag equipment and portable appliances according to the standard frequencies.
It is important to protect your employees and ensure your business is compliant with the national safety standards. Compliance with the AS/NZS 3760 and the AS/NZS 3012 will help you prevent harm at work, and ensure you have recorded evidence of your efforts to ensure a safe working environment should an accident occur.
What type of appliances needs to be tested?
You need to test all of your portable equipment including power tools and small appliances. You should always test appliances that are being used for the first time, or items that have recently been serviced or repair.
The nature of your business will determine the types of appliances you need to have tested. Your equipment might include kettles, toasters, desk lamps, power drills, circular saws, hair dryers etc.
When does the equipment need to be tested?
The testing frequency for portable devices varies according to the nature of the workplace and the type of equipment. The following information is based on the test & tag frequency standards stipulated by the AS/NZS 3012.
Construction and demolition sites:
- Portable equipment should be tested every 3 months
- Hire equipment must be tested prior to hire and at least once a month (if hire equipment remains on site then it should be tested to the same standard as all other portable equipment).
- Portable RCDs should be tested every 3 months
For the testing frequency requirements in all other work environments, see our testing and tagging services page.
Why choose Jim’s Test & Tag for portable appliance testing?
At Jim’s Test & Tag we are a professional team of electrical testing and tagging technicians. We ensure all of our team members work to the latest industry standards and are always updating their knowledge of electrical safety testing. PAT testing should only be completed by professionals who are aware of the latest testing standards. You need to hire a testing technician to complete all testing procedures for optimum safety.
We offer notification of scheduled maintenance to ensure you are up to date with your testing requirements. We have data management services in place to record all results and provide clients with comprehensive details of their testing outcomes. You can be fully informed of the testing and tagging process when you work with a Jim’s Test & Tag technician. Our team members test and tag equipment promptly, and with mindfulness of productivity in your business.
Is there a standard for portable appliance testing?
Our safety technicians complete checks with PAT tester devices maintained according to the AS/NZS 3760. It is a joint standard for Australia and New Zealand created by Standards Australia. The standard covers in-service safety inspection and testing of electrical equipment. Technicians who work to the standard will provide a log book of results and ensure the testing method and frequency of testing is adhered to.
[/vc_column_text][/vc_column][/vc_row]